Fabrication Shop Manager Job Description
A Storage System for the Wright Line Manufacturing Process, Managers of Metal Fabrication, Machine Shop Operations Managers: Experience and Benefit Expectations and more about fabrication shop manager job. Get more data about fabrication shop manager job for your career planning.
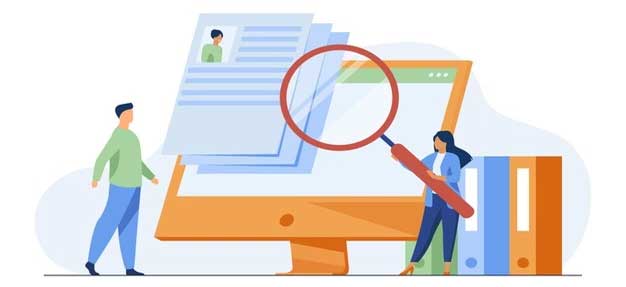
- A Storage System for the Wright Line Manufacturing Process
- Managers of Metal Fabrication
- Machine Shop Operations Managers: Experience and Benefit Expectations
- A Business Intelligence Analyst
- The Shop Manager
- Fabrication Manager
- Production Managers in a Factory
- The Store Manager
- The Bozzone View of the Custom Fabrication Job Shop
- Production Managers
- An Overview of Work Flow and Operations Management in the Construction Industry
- First Aid Equipment and Supplies for a Safe, Efficient Shop
A Storage System for the Wright Line Manufacturing Process
More than 50 employees were directed and managed in the fabrication of Wright Line product. The storage layout was designed to support company growth and reduce costs. Implemented raw material tracking software to help with inventory accuracy.
Read also our paper about Resource Manager career planning.
Managers of Metal Fabrication
Smooth and efficient processes are important for metal fabrication. Managers are often asked to analyze the current state of the factory and identify areas in which costs can be cut. The manager could compare existing suppliers with others in the market to see which offers better deals.
Changes in equipment or materials could make certain production steps obsolete. Keeping costs down is important for any business, but worker safety is more important. Managers of metal fabrication are responsible for training and refreshing employees.
Managers make step-by-step instructions and guidelines. Clear expectations are important. Employee management is more than safety.
Managers need to hire the right people. The ability to handle stress on the production floor is one of the necessary traits. Good managers can help struggling employees by showing them better ways to manage their time.
Managers must be able to handle high demand days without affecting worker's feelings. Metal fabrication is a very specialized field with a lot at stake. Managers are often the ones who help employees when the going gets tough.
Machine Shop Operations Managers: Experience and Benefit Expectations
Machine shop operations managers manage costs and expenses through process efficiency. Managers make sure the proper equipment is on hand. Job duties include analyzing and adjusting work schedules, handling quality issues, and managing customer interactions.
Your responsibility will include personnel matters. You must plan for training and skill development. Effective leadership principles must be used by shop operations mangers.
You need good communication skills and the ability to work with all levels of employees, including sales and marketing, engineering, maintenance and human resources. Since fabrication is the main function of a machine shop, you need to know how to read mechanical and electrical drawings. Knowledge of federal, state and local safety and health regulations is needed for safe use of machine tools.
Machine shop operations managers need hands-on experience to be successful. You can gain experience working in a machine shop, working with machine tools or doing similar work in a manufacturing environment over a number of years. Many employers prefer to hire operations managers with a minimum of a bachelor's degree in an engineering discipline such as mechanical or electrical.
If you have a combination of education and work experience, consideration may be given. According to Simply Hired.com, machine shop operations managers can expect to make an average annual salary of $51,000. Your earnings will be affected by a number of factors, including the hiring company, benefits package, job experience and industry sector you work in.
See also our paper on Rental Manager career description.
A Business Intelligence Analyst
You should have good people management skills and a good understanding of business operations to be a shop manager. An outstanding shop manager should be able to run a profitable shop.
The Shop Manager
Shop managers are responsible for the day to day operations of the store. The shop manager is supposed to coordinate the other staff members so that they work together to achieve company targets. Shop managers are responsible for hiring, training and disciplining staff, and it is their duty to record and manage all money coming into the store.
Shop managers account for all monetary transactions. They must establish proper money-handling procedures for the staff to follow and record the amount and source of money collected. The shop manager keeps a record of the store's spending and often distributes paychecks to employees.
The shop manager has a duty to inventory control. If an item is not selling, the manager is responsible to either return it to headquarters or put it on sale. The manager should keep a record of the merchandise in the store and order new supplies if they run out.
Detailed post on User Acquisition Manager career description.
Fabrication Manager
The job of a fabrication manager is to ensure that products meet customer specifications and quality expectations. Responsibilities include scheduling production and managing inventory. They make sure the shop stays on time and within budget.
Production Managers in a Factory
A production manager is the person in charge of all manufacturing activities in a factory. Their primary duties are to coordinate and control all the steps in the production process to make sure products are delivered on time and within the budget. Production Managers oversee all aspects of manufacturing from concept through production and delivery while also overseeing quality.
They establish, manage and lead production teams to create products that are in line with the company's environment, health and safety standards while complying with all external regulations. Production Managers are in charge of resources that go into manufactured products. Delivery and productivity targets are met when they are worked on from a factory.
They work with a lot of teams. The Factory Manager is usually the one who takes an active role in managing teams to deliver and meet output targets. They may report directly to the owners of small companies.
The role of Production Managers is the same in many industries. They usually oversee both human and material resources. Depending on the size of the company, their day-to-day activities may vary.
Detailed post on Delievery Manager job guide.
The Store Manager
The store manager is in charge of the day to day operations. Store policies and marketing programs that increase sales and grow the existing customer base are strategies that can be developed. Store standards and conditions should be maintained.
The Bozzone View of the Custom Fabrication Job Shop
There is no theory of job shops. Bozzone said that no one in the management consulting world has really looked at the job shop business model in a serious way. It is no wonder that many custom fabrication job shops struggle with on-time delivery.
The annual survey from the Fabricators & Manufacturers Association has reported on-time delivery rates in the 80 percent range for years. Many fabricators achieve near- perfect on-time delivery rates, and the yearly average comes from a wide range of responses. Just as many report rates that are below average.
Many job shops grow into organizations that ship hundreds or thousands of different parts over a month or year, each with their own demand cycles, routes, and engineering and manufacturing requirements. It all creates a web of complexity. Bozzone believes that the way most job shops are organized is related to the way they organize the business.
Bozzone goes deeper and tackles the root cause of the organization structure itself. What is wrong with it? Bozzone explained that it doesn't consider the actual business processes that define how a job shop actually works.
The founder hires more and more people as the order volume grows. The number of orders and machines grows as they get more complicated. The shop hires people.
Detailed post on Floral Manager job planning.
Production Managers
Managers at manufacturing plants are in charge of day-to-day operations. They make sure that production stays on schedule, they hire and manage workers, and they fix production problems. A bachelor's degree is typically the only qualification for production managers.
An Overview of Work Flow and Operations Management in the Construction Industry
Operations managers are responsible for an intricate job. They need to ensure a smooth flow of products in and out of the facility, as well as promote timely order fulfillment, maximize the efficiency of all procedures, and maximize the effectiveness of their operations. Operations managers have a lot to juggle for the success of their business, with a strong focus on profitability.
Some methods for improving processes can increase efficiency and reduce waste. To get more done, you need to be willing to try new things. If you can increase spatial and work flow organization, simplify your fabrication tasks, and establish guidelines for data collection, your company can begin to see improved efficiency, higher productivity, and less waste in no time.
It's difficult to improve your fabrication process if you don't know your current work flow. To get a good idea of your current operations, identify everything that is needed to make a product, including the processes, people, and technology, as well as the communication, procedures, and resources necessary throughout the company. Make sure employees are trained to fix issues immediately when there is a mistake, rather than waiting for the next shift to take over.
Make sure employees have easy access to equipment and tools by organizing your shop floor. The spatial organization of materials, tools, and manufacturing space cuts down on time spent moving and searching for items. It is negatively affects your business if machinery breaks down on a consistent basis.
It is important to service your fabrication equipment. A preventive maintenance process will help catch problems before they become too serious. It is not possible to maximize your fabrication process with new machines or new employees.
Read also our post on Casting Manager job description.
First Aid Equipment and Supplies for a Safe, Efficient Shop
In case of an accident, make sure your shop has all the safety equipment and first aid supplies. Train your employees in first aid. Quality results will only be ensured by buying quality equipment.









X Cancel