Factory Manager Job Description
A Top-Performance Factory Manager, Factory Management, The wages of factory managers, A Simple Way to Train Quality Engineers, The Factory Manager role at a leading company and more about factory manager job. Get more data about factory manager job for your career planning.
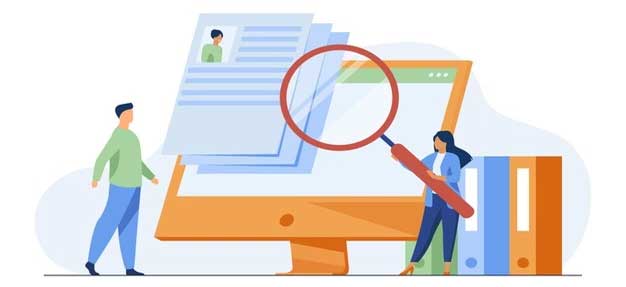
- A Top-Performance Factory Manager
- Factory Management
- The wages of factory managers
- A Simple Way to Train Quality Engineers
- The Factory Manager role at a leading company
- The Factory Manager role in a dynamic environment
- Stewardship in the Plant
- The Workforce of a Manufacturing Manager
- A Survey of Leadership Skills in Production Managers
- A Highly Experienced Supervisor
- Factory Managers
- The Effect of Manufacturing Managers on the Workforce and Performance in a Large Organization
- Production Managers: A Knowledge-Base Perspective
- The Operations Manager
- General Managers
A Top-Performance Factory Manager
Factory managers make sure that factory operations run smoothly. They work in manufacturing plants to make goods such as electronics, cars, equipment, and packaging. To be successful as a factory manager, you need to have outstanding problem-solving skills and resolve any issues that may derail production. A top-performing factory manager should have good communication, management and leadership skills to ensure that factory operations run smoothly.
Read also our article on Benefits Manager career guide.
Factory Management
A factory manager is the most senior manager in the factory and is responsible for all the activities of the factory. The amount and quality of the items that the factory is producing are tied to the objectives of the factory manager. Some factories are open 24 hours a day.
Factory managers have a wide variety of skills because they have offices and production lines. Ensuring that there is no down time and that everyone is working at a reasonable pace is a key to effective running of a factory. Companies don't want their staff to be standing around and not doing anything.
The wages of factory managers
Factory managers are usually required to have at least five years of experience, and they run the factory when senior management isn't on site. The demand for industrial production managers is set to remain at the current level through the year 2026 according to the National Bureau of Labor Statistics. Most factory managers have a bachelor's degree in a related field.
They study the principles of economics, basic logistics and organizational communication. Their years of experience working their way up from a factory worker is what most of their technical knowledge comes from. The national median salary for factory managers is $83,700.
The top 10 percent of the population make more than $140,000, while the bottom 10 percent make less than $41,000. The Supply Chain Management Review is a trusted digital publication in the supply chain management industry. It is updated daily with articles relevant to workers and factory managers.
Detailed study about Document Imaging Production Manager job description.
A Simple Way to Train Quality Engineers
If they are well behaved and not easily influenced, they could be sent to suppliers. If a supplier Quality Engineer just does an audit of a process, they don't need to be paid a salary.
The Factory Manager role at a leading company
The company that the Factory Manager will join has made them the leader in their field. The scope of the offer, the size of the business, the freedom and autonomy to drive your career forward all add up to a great place to work.
A good post on Safety & Security Manager job guide.
The Factory Manager role in a dynamic environment
As a Factory Manager, you will be responsible for overseeing the performance and giving work to workers. Ensuring that the targets are met is your responsibility. Good leadership abilities and a positive work environment are also important.
Stewardship in the Plant
The plant manager will make sure policies and procedures are followed in all operations. They develop processes that maximize stewardship.
Read our paper about Assistant Housekeeping Manager career description.
The Workforce of a Manufacturing Manager
The manufacturing worker has to be able to think on their feet and fix small problems as they arrive. All of the day's issues can't be solved by supervisors. Managers of manufacturing companies look for employees who can make sound, in-the-moment decisions when unforeseen issues arise.
A Survey of Leadership Skills in Production Managers
Excellent leadership skills are a must for a Production Manager who will be responsible for leading teams in fast paced environments. Being a successful Production Manager requires having the ability to communicate effectively and efficiently, as well as providing clear direction to supervisors, team leaders and operatives. You will need to motivate staff in high pressure situations to ensure production targets are met.
It is almost certain that a hiring manager will ask about your leadership skills during an interview. You should have examples of situations where you were successful in leading teams and had a difficult relationship with a subordinate. Managing large teams of staff on multiple projects is not easy and having exceptional organisation skills is a must for a successful Production Manager.
Potential employees are asked about examples of their strong organisation skills. You should have examples of when you prioritised your work to ensure that the objectives were met. A strong Production Manager needs to be able to work under pressure and motivate others to meet deadlines.
Negotiation is a key factor when trying to become a Production Manager. Powerful negotiation skills and tactics are important when working in a production environment as you will be dealing with your team, managers, clients and suppliers all whilst working within tight deadlines and budgets, a hefty task for anyone! A good negotiator can close the best deals, improve supplier relationships, and manage conflicts effectively.
Read also our post about Analytical Validation Manager job guide.
A Highly Experienced Supervisor
A factory manager with over 10 years of experience. In order to achieve optimal productivity and results, skilled in supervising, leading, and directing tasks. Experience in prior positions has helped develop the ability to balance high productivity with high quality and effectively manage the personnel on the factory team.
Factory Managers
Factory managers are hired by manufacturing plants to make sure that orders are completed on time. They are in charge of factory workers and execute strategies to improve their work.
Detailed post about Ar Manager career planning.
The Effect of Manufacturing Managers on the Workforce and Performance in a Large Organization
A manufacturing manager is in charge of the production process. The manufacturing manager divides his time between the office and the production area of the company to make sure that all workers and departments meet the productivity and efficiency standards of the organization. The Department of Labor says that employment of manufacturing managers will decline by 8 percent over the next decade.
Production Managers: A Knowledge-Base Perspective
A Production Manager is a person who makes sure that manufacturing equipment and tools function properly. Their duties include building production schedules, making sure production processes stay within budgets and deadlines, and reviewing the productivity of an organization's manufacturing equipment. A production manager is a supervisor who oversees the production process to ensure it stays within budget.
They are responsible for finding ways to improve the organization. Production Managers will review employees and equipment to find ways to improve. They will work with team members to build strategies.
Production Managers will work with other departments and team members to set goals. They are in charge of scheduling maintenance to keep equipment running. Production Managers who want to be promoted to management often need up to 5 years of experience in other areas of production.
They should have at least 2 years of experience in the role. Production Managers can get a good experience by having a track record for excellent project management and employee training. There are a few differences between the two roles when it comes to their responsibilities.
Production Managers will make the raw products into usable products. They usually take care of the big picture and scheduling the items that are involved in the manufacturing process. Manufacturing Managers are usually in charge of more hands-on tasks to improve the operations of the machines.
See also our column about Fitness Manager career guide.
The Operations Manager
The operations manager has specific duties such as formulating strategy, improving performance, procuring material and resources and securing compliance. You should be prepared to mentor your team members, find ways to increase quality of customer service and implement best practices across all levels.
General Managers
General managers are tasked with overseeing daily business activities, improving overall business functions, training heads of departments, managing budgets, developing strategic plans, creating policies, and communicating business goals.









X Cancel