Quality Control Manager Job Description
A Quality Control Manager, A Review on Quality Assurance Processes, Quality Management, The Role of Quality Control in the Textile Industry and more about quality control manager job. Get more data about quality control manager job for your career planning.
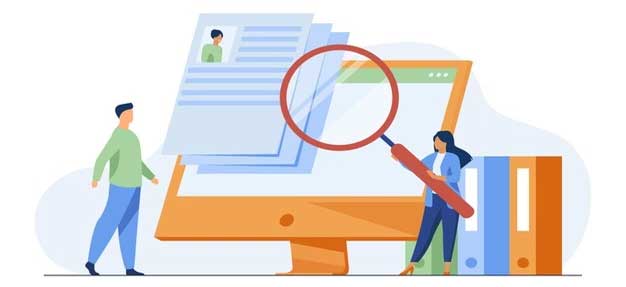
- A Quality Control Manager
- A Review on Quality Assurance Processes
- Quality Management
- The Role of Quality Control in the Textile Industry
- The role of the personnel in ensuring that test results meet specification
- The Quality Control Manager at a Linear Plant
- A Master's Degree in Quality Control
- Quality Management of a High-QED System
- Quality Assurance Managers
- Anomaly Detection and Management Skills for Quality Engineers
- Quality Control Managers
- Better MRO: A Review of Quality Control Manager Jobs in the Manufacturing Industry
A Quality Control Manager
A quality control manager is in charge of product development procedures. The quality control manager will work with clients to make sure the final products meet their needs. Excellent communication and listening skills, as well as strong observational, analytical, and problem-solving skills, are required for successful quality control managers. You should be skilled in understanding scientific and technical data.
Read our column on Growth Marketing Manager career description.
A Review on Quality Assurance Processes
Quality assurance is the process of making sure that the product developed is in line with the standards set by the organization before it is launched into the market. The customers consider the organization's reputation when deciding if a product should be sold. Quality assurance professionals should have a good understanding of the organization's processes.
It is important to have basic knowledge to decide if the product is up to the mark. The domain knowledge will help you figure out where the problem started. Clear verbal communication skills will help you to explain the process and improve it further to attain quality standards.
It is important to have proficient written skills to prepare documents. Quality assurance protocols and processes can be implemented with project management skills. Quality assurance professionals will be impacted by changes to processes like implementing new technologies.
Quality Management
Quality management is the performance of managing activities and responsibilities within a system to make sure that products and services are compatible with means used to produce them. It is used to manage and have an aspired level of quality. Product improvement, method improvement, and people-based improvement are elements of quality improvement systems.
There are methods that can be used. They include the Toyota Production System, Kansei Engineering, and the BPR. Quality assurance managers have to wait off of internal, external, and international laws and regulations about manufacturing, trading and freight goods.
Managers base their processes on a standard such as ISO 9000 Quality Management, issued by the International Organization for Standardization. Industry-specific manual and protocols are implemented. The American Society of Brewing Chemists has terms for the processing of beer.
There can be slight differences in material calibrations or malfunctioning pH meters. As a quality support manager, you would manage teams of investigators who evaluate products and their ingredients at various stages of creation. Managers give supervisors with documented quality criteria as guidelines for their day-to-day work.
Quality review tools and software used by managers. If you understand product errors or place safety defenders off a conveyor belt, you will have the authority to stop the production order. Quality assurance managers implement training for the workforce and ensure that workers are aware of quality specifications, as well as being a quality assurance supervisor.
Detailed paper on Video Manager job description.
The Role of Quality Control in the Textile Industry
The apparel industry is growing because of the higher demand for garments. The garment's maker should give a quality product. Every factory has a quality control department.
The role of the personnel in ensuring that test results meet specification
The purpose in the end is the same despite the different roles. The test results must meet the acceptance criteria established by the specification and be reliable because the procedures used were in line with the standard. There will be less opportunity for non-conformities, resulting in lower costs and on-time delivery, if roles and responsibilities of the personnel are understood. The owner will have a quality product that maximizes the asset's service life at reduced overall costs, while the contractor will keep their reputation for providing quality work that helps ensure a continuous revenue stream.
Don't miss our report on Channel Marketing Manager job planning.
The Quality Control Manager at a Linear Plant
The Quality Control Manager is an important part of the team and helps define and carry out appropriate tests and inspections to confirm a product complies with quality standards. The job of inspecting incoming materials and documenting test results is important. The Quality Control Manager is responsible for ensuring that the plant follows and complies with quality protocols.
The Quality Control Manager is responsible for the management of quality technicians. Responsibilities include cost efficiency, continuous improvement on processes, service, and safety for an entire business unit across all shifts. The Quality Control Manager works with production, maintenance and warehouse teams to communicate quality procedures and develop sustainable practices to maintain superior quality process.
Quality Control Manager is responsible for inspecting all products and determining what is acceptable and what is not. Products that are acceptable are released to inventory or rejected. The quality management program is overseen by the Quality Control Manager.
A Master's Degree in Quality Control
To work in a quality control related profession, graduates need to strengthen their research and development skills. Their studies should lead them to look at the various aspects of developing new products and machines. Quality control testing procedures and computer simulations can be reviewed in courses such as Engineering, Mathematics, Statistics and Quality Assurance. You should get a Masters Degree if you want better job opportunities.
Don't miss our article on Fast Fit Manager career planning.
Quality Management of a High-QED System
The final product will be inspected by the Quality Manager to make sure it complies with legal standards and is in line with customer expectations. A quality manager is thorough and attentive.
Quality Assurance Managers
Quality Assurance Managers have good experience in quality control. The ideal candidate is a reliable and competent professional who can approve the continuation of a business life cycle.
Read also our story on Manager Of Data Analytics job planning.
Anomaly Detection and Management Skills for Quality Engineers
The ability to analyze the data with a keen eye is a critical skill for a quality assurance manager. A manager of a team should guide them and recognize hidden errors instead of just proving that an application is working. As a quality assurance manager, you should be able to detect anomalies and guide your team on how to resolve them.
He will have to take a quick look at the application and check if anything looks off when compared to the requirement specification. When it comes to the way they are doing things and doing their job, people don't like change. You must be able to adapt and influence to be considered a highly relevant skill for the managers.
Their job is to find ways to make the team work faster. In the current age of Agile, you must change to ensure that your team does not lag behind in comparison to others. It is important to encourage your teammates and colleagues to adapt the same for better productivity, individual output, and collective delivery as you bring something new on-board.
If you want to become a good manager, you should be able to adapt to the Agile world and keep up with your work. Whenever a change in the requirement arrives, you must be prepared to deal with it. The blame will come upon you if your team is not able to deliver the work on time.
In the current world of Agile and DevOps, time management is a must have skill for a manager. The management does not have to extend the deadline if you and your team are ready with the deliverables. In the first scenario, a good manager of quality assurance should be able to fight with the management to explain why they are doing the right thing and how letting a critical defect go unfixed will impact the product or company's reputation in the long run.
Quality Control Managers
Quality Control Managers with advanced degrees can be promoted easily. They can become an independent consultant. Many organizations need experienced professionals to improve production quality, reliability, and reduce production costs.
Quality Control Managers are not responsible for monitoring the quality of the products but are responsible for monitoring whether the products are necessary for the production process. They work with other departments to make sure the product met the desired standards. To be a quality control manager, they have to regularly upskill and reskill by taking up industry-recognized quality management training programs to coordinate with other quality management professionals.
Don't miss our report about Enterprise Account Manager career guide.
Better MRO: A Review of Quality Control Manager Jobs in the Manufacturing Industry
A review of job listings for quality control managers in the manufacturing industry shows that companies look for more than just manufacturing and computer numerical control knowledge. The quality control manager focuses on operations practices and ways to help drive up productivity and improve work processes that will reduce costs while also ensuring that parts and products adhere to desired quality specifications. Quality control managers can start their careers in a number of roles, including as a member of the inspection team, as a product engineer, or as an assistant quality control manager.









X Cancel