Quality Systems Coordinator Job Description
Quality Coordinators, The Post Graduate Career in a Systems Coordinator, Quality Management System, The Quality Assurance Specialist Position in the United States and more about quality systems coordinator job. Get more data about quality systems coordinator job for your career planning.
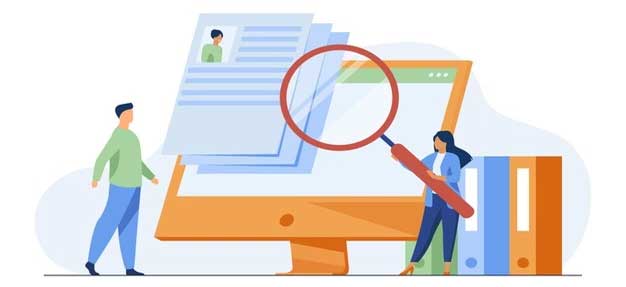
- Quality Coordinators
- The Post Graduate Career in a Systems Coordinator
- Quality Management System
- The Quality Assurance Specialist Position in the United States
- ISO9001:2015 - A History of Quality Management Systems
- The Role of Quality Management in an Enterprise
- ISO-9000 Coordinators
- The Role of Nurses in Quality Improvement and Patient Care
- The Role of Humans in Quality Assurance
- Time Management for Software Quality
- The Role of Quality Control Specialists in Manufacturing
- How to write a Quality-Assurance Specialist resume
Quality Coordinators
To be successful as a quality coordinator you should be able to ensure that all materials, processes, and procedures meet regulatory and quality standards and promptly resolve any issues or discrepancies that may arise.
Detailed post about Recruiting Coordinator job planning.
The Post Graduate Career in a Systems Coordinator
A systems cosutr must know how to communicate with other employees in other branches about policies and procedures in the area of records management. A systems coordinator's main job is data processing and strong computer skills are a plus. A systems couner must be able to fix office systems.
The duties of an administrative coordinators are similar to the systems coordinators. The average annual salary for a systems coordinators with less than one year of experience is $29,948. The Bureau of Labor expects the growth rate for employment as a systems coordinators to be 11 percent between 2008 and 2018, with the majority of the growth coming from health care and information systems management.
Quality Management System
The information collected, organized, monitors and distributed may include compliance to and documentation of quality management standards, such as ISO 9001. Reports are typically generated using computer skills and distributed to various users in the organization. Oversees all aspects of an organization's quality or business improvement efforts, such as developing and administrating the program, training and coaching employees, and facilitating change throughout the organization.
Quality improvement efforts will meet or exceed internal and external customers needs if a strategic plan is established. Operates in support of or under the supervision of a Six sigma black belt, analyzes quality problems and is involved in quality improvement projects. Has at least three years of experience.
The administration of an organization's quality, process or business improvement efforts within a defined segment of the organization is ensured. It is possible that this person is responsible for dealing with customers and suppliers on quality or performance issues. Typically, there is direct reports.
Quality expert is responsible for strategic implementations within an organization. I am qualified to teach Six sigma methods, tools and applications in all levels of an organization. Is a resource for statistical methods.
Engineering work is done to evaluate manufacturing processes or performance improvement projects. The development of processes may be included in the duties. Quality assurance process sampling systems, procedures and statistical techniques are installed.
Don't miss our paper about Test Systems Engineer career guide.
The Quality Assurance Specialist Position in the United States
The primary tasks, duties and competencies associated with ensuring that the product meets the required quality standards are well defined for the quality assurance specialist position. The average quality assurance analyst salary in the USA is $68,463 per year, according to Indeed.com. The average salary for a quality assurance manager is $75,087 per year.
ISO9001:2015 - A History of Quality Management Systems
ISO 9001:2015 is the international standard specifying requirements for quality management systems. The ISO 9001 standard is referred to as "QMS", but it is actually the entire system. The documents are only used to describe the system.
The most recognized quality management system standard is ISO 9001:2015. Organizations can use the requirements for a QMS in ISO 9001:2015. The best way to deploy is to break each process down into subprocesses and educate staff on documentation, education, training tools, and metrics.
Quality management systems are being deployed using company intranets. The quality management system is mostly accomplished through routine audits of the system. Depending on size, potential risk, and environmental impact, the specifics vary greatly.
Craftsmen began organizing into unions called guilds in the 12th century. Quality management systems were used to control product and process outcomes. Quality results were needed as more people worked together to produce results.
Quality became more important during World War II when bullets made in one state had to be made in another. The armed forces inspected every unit of product. Quality techniques of sampling for inspection were used by the military to simplify the process without sacrificing safety.
A good paper on Billing Coordinator career description.
The Role of Quality Management in an Enterprise
There's more to quality than just making things without defects or trains running on time. To survive and thrive. Quality can enhance your organisation's brand reputation, protect it against risks, increase its efficiency, boost its profits and position it to keep on growing.
All while making staff and customers happy. Quality is more than just a box to be satisfied with. Failures resulting from poor governance, ineffective assurance and resistance to change can have dire consequences for businesses, individuals and society as a whole.
Quality is an issue for other businesses. Quality management is about meeting the needs of different stakeholders, which is what every organisation has. Everyone from the CEO to the intern is responsible for the quality of their work.
Different people have different responsibilities and influence over things that affect the quality of an organisation's outputs. They come in many different guises. Many people have titles such as quality manager, quality engineer, quality director assurance manager, while others deal with aspects of quality as part of a broader remit.
Some are concerned with the delivery of products and services, while others are part of the leadership of their organisation. Some are employed in-house, while others are outside the organisation they work for. There's a lot of help when it comes to quality.
ISO-9000 Coordinators
A quality system is a series of processes that come together to make something happen. Identifying customers expectations is the starting point. Customers can count on a product or service to meet their needs.
Customers quickly discover that companies that don't have effective quality systems can't be relied on to deliver good quality products and services. Quality-system coordinators prevent that from happening. ISO-9000 is a best-practice approach that makes customers happy and will keep them coming back.
ISO-9001 is a set of criteria that describes the minimum requirements for establishing a quality system that works. To make sure that ISO-9001 is integrated into all key processes, and to accurately interpret how it applies across the company, a quality-system coordinator will be called upon to understand it. A quality-system coordinator uses audits to verify the company's system meets best-practice criteria.
Internal audits are performed to make sure that what is being done is in line with what should be done. Many companies use external audits to show their customers that their systems meet best practices. The coordination works with external auditors from initial planning to the performance of the audit, and follows through with any corrective actions that might be needed as a result.
Read also our paper about Accounts Receivable Coordinator job description.
The Role of Nurses in Quality Improvement and Patient Care
A survey of quality improvement coordinators by Payscale.com shows that the average salary is $91,800. The quality improvement coordinators with 5 to 10 years of experience will make an average of $69,000 a year. Senior quality improvement coordinators with more than 10 years of experience earn an average of $71,000 a year, but after 20 years of experience, they will earn about $72,000 a year.
The quality improvement coordinators are responsible for working with the hospital or clinic to achieve quality improvement goals. They are usually responsible for ensuring that staff members conform to government regulations. The cosmetologists are responsible for investigating any claims against their organization, including malpractice or failure to adhere to recommended safety or institutional standards.
The quality improvement program is overseen by the coordinators and he develops performance improvement targets. The coordinators must use nursing experience and education to manage staff and data and measure progress. The cosmetologists must be experienced in developing charts and graphs representing key performance indicators and other data.
Quality improvement coordinators need project management training and skills. The person who is the coordinators should have training and knowledge of continuous improvement principles and the ability to interpret and take action patient care data. Many job descriptions request that the coordinators be self-motivated and self-directed.
Communication skills are required because the coordinators report to the medical directors. In a large hospital or clinic setting, master's degrees in healthcare administration or nursing specialties are often desirable. Master's degrees in health information management or health informatics are required for quality improvement coordinators.
The Role of Humans in Quality Assurance
If you work in quality assurance, you know how quickly emerging technologies are changing the nature of your work. The internet of things, machine learning, andRFID tracking are just a few of the new disruptive technologies that are almost certainly going to impact your career in one form or another in a few years. Quality assurance is about preventing a bad product from being produced and keeping it from reaching the consumer so that it can do harm.
Quality assurance workers who demonstrate an ability to understand interpret data have an advantage over those who don't. Those who can take the data, boil it down, and use it to communicate with other people have the greatest advantage. Quality assurance processes and protocols can be implemented with project management skills.
When a company makes significant changes to their processes, project management can affect the quality of the process. Implementing any of the technologies poised to impact the work done by quality assurance teams will be no easy feat. Incorporating them in the supply chain will require a solid foundation in project management and a good understanding of both the QA process and the supply chain.
Quality assurance workers should develop specific industry expertise to increase their job security as more of the job is automated through the use of technology. Being effective in quality assurance requires an understanding of how the product affects humans. It requires a sense of what is at stake if bad product leaves a facility.
It requires a level of compassion for the end users. Big Data, machines, and robots are tools. Quality assurance processes will be helped by them.
A nice report on Product Development Coordinator job description.
Time Management for Software Quality
Managing your time well will ensure you have enough time to complete your tasks and confirm they comply with specifications. It reduces stress and makes it easier to complete your duties. When you meet your deadlines, you also make sure others who rely on you have enough time to meet their own deadlines without affecting their work quality.
Problem-solving skills can help you find solutions if you are struggling to meet quality standards. When challenges arise in your duties, a combination of creativity, logic and critical thinking can serve you. Communication skills that are strong can help you explain how to improve processes to other people.
Your listening skills are important for understanding what your colleagues need from you. Strong written communication is a must for software testing and other quality assurance roles. Quality assurance requires understanding quality standards.
Employees are expected to work within the company's standards. Understanding the guidelines set by the Food and Drug Administration can help you meet quality expectations. Supplemental training can teach you new practices and remind you of some techniques you may have overlooked.
The Role of Quality Control Specialists in Manufacturing
Quality control specialists are part of a manufacturing team and are responsible for maintaining records of defects and ensuring that parts are repaired, re-tested or pulled from production. They can deliver their reports to other team members to address quality issues. Quality control specialists are usually tasked with testing and assessing products in an industrial or warehouse setting.
The quality control specialist can test parts or products using a variety of techniques, checking that specifications are met and that the product works as intended. A quality control specialist is often tasked with testing products and packaging in a lab or on the production floor to ensure consistency. The Bureau of Labor Statistics says that the median wage for quality control inspectors is $36,780.
The top 10 percent earn over 63,590 annually, while the bottom 10 percent earn less than $21,880. Quality control specialists will be in demand less by the year 2026 as manufacturers increasingly rely on automated quality control systems and 3D scanning to quickly identify defects. Quality control specialists are still used in some industries.
Read our paper about Social Services Coordinator career guide.
How to write a Quality-Assurance Specialist resume
Quality Assurance is part of the manufacturing quality system. It is process oriented and focuses on eliminating all process variation by creating, revising and strictly implementing a set of tightly and precisely defined process and procedures that when exactly followed, ensure the final quality of the product. Quality Assurance is preventative.
Quality Assurance is operating at the level of manufacturing processes and procedures. Quality Assurance is not concerned with measurement or inspection of the finished product, but with Quality Control, which is the role of Quality Control. Many of the techniques and approaches used in quality assurance were developed for the manufacturing industry, but they are also used in other sectors such as customer care, software development, aviation, oil and gas, regulatory compliance, etc.
The path to becoming a Quality Assurance Specialist is dependent on the sector you are working in and can be very varied. The key attributes of candidates can be found in high school or secondary school level education, industry knowledge and experience, and also in the degree of education. Quality Assurance Specialists have a certain level of education, but it's not as important as the skills and personal qualities that come from them.
Candidates showing the right skills and qualities will be given on-the-job training by many companies. Tailoring your Quality Assurance Specialist resume to reflect the language used in the job advert is very important. If you have relevant experience or skills, use the words and phrases that the employer has used to describe them.









X Cancel