Logistics Planner Job Description
The Association of Logistics Planners, Dead Miles: How to Keep the Luggage Down, The Logistics Manager: A Role of Independent Carriers in Organizational Management and more about logistics planner job. Get more data about logistics planner job for your career planning.
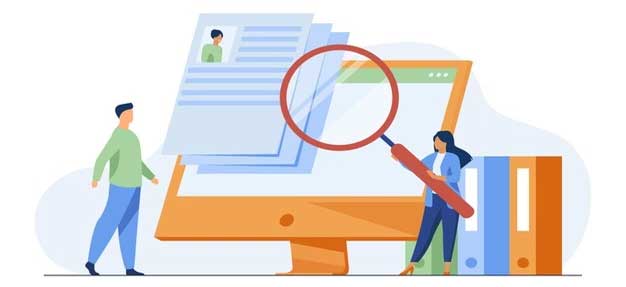
- The Association of Logistics Planners
- Dead Miles: How to Keep the Luggage Down
- The Logistics Manager: A Role of Independent Carriers in Organizational Management
- The Construction Logistics Manager
- Experience in Logistics: A Must-See Before Applying
- A Top-notch Supply Planner
- Supply Chain Planning
- A Job Search in Logistics Staff
- Hiring a Production Planner: A Job Description
- Communication Skills in Logistics Management
- What Skills Should You Include in Your Resume?
- A Business Intelligence Analysis of Logistics Management
- A Shortcut to the Road?
- Supply Chain and Logistics: Where to Start?
- The Job Types in Supply Chain and Logistics
- ProjectManager.com: A Project Management Software for Managing Supply Chains
- The Logistics Team of the ACS Supply Chain
- A qualification in load planning
- A Comprehensive Logistics Strategy for Business
The Association of Logistics Planners
The role of alogistics planner is a supervisor. They make sure the employees involved in the shipping or receiving process perform their assigned tasks up to standard. The VP of logistics in a large company may have a Logistics planners answer.
The National Bureau of Labor Statistics says that demand for logisticians will rise 7 percent through the year. Logistic planners have to determine the size and scope of the project before any products come in. They use their project management skills to determine the resources and labor needed for a project, how much the project will cost, and how long it will take to complete.
Logistics planners meet with suppliers or clients to work out the details of delivery, such as price, quantity, what products are being delivered, and the time frame for delivery. The national median salary of alogistics planners is over fifty grand. The bottom 10 percent make less than the top 10 percent.
The Council of Supply Chain Management Professionals has a lot of resources for members. There are online courses that are relevant to logistics planners. The International Society of Logistics has members in more than 50 countries.
It offers great networking opportunities on a global level. Every year there is a conference for each chapter. The Association for Supply Chain Management is not specifically for logistics, but it has many planners.
A nice paper about Production Planner job description.
Dead Miles: How to Keep the Luggage Down
Exactly right, Melonlity. The trucking industry hires a lot of engineers because of that. It makes sense to use engineers in logistics when you start thinking about it.
Thelogisticsplanner is one of the most important people in the company. Why? The trucking industry is very competitive and the companies with good logistics make a profit.
Take dead miles. Those are miles in which a truck runs without a load. A good logistics manager can keep dead miles to a minimum.
The Logistics Manager: A Role of Independent Carriers in Organizational Management
Most organizations will have to rely on the services of independent carriers if they have their own transportation and delivery system. The logistics manager is required to coordinate with carriers for the shipping of people and goods, including understanding the carrier's capabilities and negotiating the best rate. A good logistics manager will plan according to the best information available to him, but will always be prepared to adjust if conditions change.
A good column about Logistics Operations Manager job planning.
The Construction Logistics Manager
The constructionlogistics manager is responsible for all aspects of the project's logistics supply chain, stores management, development and optimisation. The control site facilities management and the movement of people, goods and equipment will be managed by thelogistics manager. The project planners, commercial managers and the senior construction manager are some of the key interface that the logistics manager must ensure early engagement with. The construction team should be aware of the support activities in support of the build program.
Experience in Logistics: A Must-See Before Applying
The logistics officer job description requires planning the set-up of project sites, as well as coordinating, directing, and monitoring activities of employees, contractors, and others involved in executing an assigned project. The work description for thelogistics officer requires a plan for the movement of materials, heavy equipment, and light trucks, as well as workforce and parts supply in compliance with the project requirements. If you have experience working as a logistics officer and are preparing a resume for another job, you should include the professional experience section to highlight the duties you have performed.
See also our report on Senior Logistics Analyst job description.
A Top-notch Supply Planner
The supply chain planners are part of the logistics department of a company. They are supposed to maintain stock levels to make sure the business runs smoothly. They perform stock inspections, anticipate market changes, and make sure inventory levels are financially feasible.
Supply Chain Planning
Supply chain planners look at current processes and determine methods for improvement with regard to cutting costs, controlling and replenish inventory, and shipping products. They respond to unexpected events and fix breakdowns along the chain. A supply chain planner knows that finding new efficiencies can mean going with a new vendor that doesn't deliver on promises or choosing a cost-saving shipping path that delays delivery to the end customer.
They know that some changes in the supply chain can be risky, but they are able to manage those risks effectively without losing sight of their job purpose. Endpoint delivery requires human hands and judgment as well as some factors beyond anyone's control. They plan for safety in mind.
Staying up to date on destination factors such as snow and ice, which could delay package shipments and jeopardize driver safety, is just one of the concerns. They encourage warehouse staff to be safe. Supply chain planners use technology and data to create reports that detail efficiency and areas for improvement.
See also our report on Logistics Supervisor job description.
A Job Search in Logistics Staff
Alogistics staff works for a company or an organization. They are responsible for supporting the co-ordination, planning, and execution of supply chain operations. They may be involved in providing support to the logistics manager in all aspects of warehouse operations, or they may be involved in working in the area of shipping and receiving functions.
The staff of the Logistics department may be responsible for documentations, including preparing paper works for outbound shipments, and reviewing shipment documents such as BOL, invoices, and packing lists. Logistics staff compare what has been received with the order to make sure the materials are in good condition, and file all necessary documentation in the warehouse. If you are looking for a job in Logistics staff, you should know that recruiters will want you to meet certain requirements before you can get the job.
Hiring a Production Planner: A Job Description
The production planners duties and responsibilities shared above can be used to complete the professional experience section of your resume and increase your chances of getting an interview with the recruiters. Recruiters look for people with the right qualities to perform the duties of the production planner role. If you are a HR manager or a scrutineer looking to hire a production planner in your company, you will need to make and publish a detailed description of the job to inform interested individuals of the duties and responsibilities that will be assigned to the success candidate.
A nice article on Logistics Management Specialist job description.
Communication Skills in Logistics Management
Communication and negotiation skills are important for a Logistics Coordinator. They are well-versed in supply management practices. The ideal candidate will have a good record-keeping and customer-oriented approach.
What Skills Should You Include in Your Resume?
If you have a strong skills section your resume, you will be in a better position to get the job you want. You need to know the top skills that recruiters look for in a resume.
A nice story about Sr. Logistics Manager job guide.
A Business Intelligence Analysis of Logistics Management
As a logistics manager, you must be able to make accurate predictions of the possible needs of your company and the outcomes of actions in the entire supply chain. You can act faster, see risks that may arise, and develop contingency plans for problems that may or may not arise with the skill that you have. Think and plan.
It is better to be safe than sorry. A graduate of a mathematics or statistics degree is not necessarily required for a good logistics manager. If you know how to read and analyze datand make interpretations that are useful to the company, you will make a fine career in logistics.
There are many universities and institutions that offer master's degree programs in data science for those who want to take their skills to the next level. Being an effective logistic manager requires you to be aware of the latest trends in supply chain. A good start for a logistics manager is taking a look at how class is determined and how to calculate freight class.
The freight class decides pricing. As a logistics manager, you must ensure that your company's supply chain is running in the most efficient way. Take time to research other companies and benchmark their practices.
A good logistics manager knows that the success of the supply chain is a group effort. Forbes offers some ways to be a leader, but you can start by allocating tasks wisely, paying attention to the team's efforts, and learning to commend good work among your teammates. It is important to treat everyone with respect and professionalism when working with other teams or units.
A Shortcut to the Road?
Mainstream management careers in Logistics and Transport Management will face the full range of management challenges. Those with the right skills are in high demand. Sounds like a tall order. Common sense and a positive attitude will take you a long way in a rewarding and satisfying career despite the rapid rate of change in Logistics and Transport.
Detailed column about Assistant Event Planner career planning.
Supply Chain and Logistics: Where to Start?
College students, job seekers, and career-changers are in the perfect time to explore their options in the growing fields of supply chain and logistics. How can you start?
The Job Types in Supply Chain and Logistics
It is best to categorize the job types in supply chain and logistics so that they are easier to understand. The supply-chain Plan, Make, Source, and Deliver model is what we are looking at. It is easy to forget that the production environment is a part of the supply chain.
It could be that you already work in manufacturing or production and have plans to move into a different area. If so, you are in a good position to do so. If you want to take on more responsibility in the supply chain, you can leave the manufacturing function and become a distribution, or supply chain manager, and then go to a senior management role.
The inbound supply chaincludes procurement, sourcing, and purchasing functions, which is a great place to learn how sales, service, and inventory management, and logistics mesh together in balancing supply with demand. You can strike out for other areas of supply chain management at any time. It is not uncommon for professionals in the supply chain to move sideways into logistics management.
ProjectManager.com: A Project Management Software for Managing Supply Chains
Logistics management is a process of organizing and implementing an operation. The flow of work from the beginning to the end is what determines the success of your business. Logistics management is done across industries.
Its goal is to manage the fruition of project life cycles. Business Logisticians have evolved into something called supply chain Logisticians as businesses grow more complex. The more steps, the better.
By considering every stage of the product, its distribution and return of materials and supplies, you are more likely to increase efficiency and increase revenues. That is one benefit of logistics management. Visibility in the business' supply chain is something it helps to create.
Logistics managers can better manage the flow of materials and avoid disruptions by analyzing historical data and tracking the real-time movement of goods. Revenue can be driven by logistics management. It improves customer service, adds to the company's reputation and brand, and in turn creates more business.
With more visibility into the supply chain there is the chance to save costs in operations, by controlling inbound funds, keeping inventory at the right level and organizing the reverse flow of goods. Logistics is just planning. Successful logistics managers understand the importance of a project management software tool to help them collect, organize and move items from one place to the next efficiently.
The Logistics Team of the ACS Supply Chain
There is plenty of jobs in the supply chaindustry. Everything in the supply chain can be incorporated. Management, strategy, planning, logistics, manufacturing, and quality control are all part of the supply chain.
The logistics team handles all the details of coordinating the complex operations associated with the supply chain. VP of Logistics, VP of Distribution, and Director of Logistics are some of the job titles. The inventory planning team makes sure the right amount of items stay on hand.
A qualification in load planning
Load planners control the transfer of freight around the country. It would be your job to make sure goods are moved in the most efficient way, taking into account schedules, costs, and health and safety. Employers will ask for a good standard of general education and some may ask for a GCSE in English and maths, but you don't need any qualifications to start work as a load planner.
A Comprehensive Logistics Strategy for Business
According to Harvard Business Review, an estimated 70% of business strategies fail due to poor execution, making effective logistics planning and strategy paramount to your company's success. A comprehensive logistics strategy should include strategic, operational and tactical levels of logistical planning, as well as the four main pain points in the supply chain, including facility locations, customer service levels and inventory and transportation decision-making. The primary goal of any strategy is to deliver the right products to the right customers at the right time and at the least cost.
An effective strategy for Logistics can help your company reduce costs by defining the service levels that are most cost-effective. The result is a win-win situation: your company benefits from cost efficiency, and your customers get what they need, when they need it. Logistics planning helps companies to anticipate change and develop strategies to adapt to it.
Many companies develop strategies for specific product lines, geographic regions or customer segments to adapt to market changes, so they can maintain efficiency across others. An effective logistics strategy involves aligning your goals to larger objectives. According to Trissa Strategy consulting, more than half of successful companies have every business unit aligned to their corporate strategy.
A majority of successful companies build their budget around their strategy, making elements such as financial forecasts, capital requirements and analysis of operating costs and cash flow vital to their company's success. There are 9. Make informed predictions by studying the needs of your supply chain.
Many manufacturers practice demand-driven logistics because they are focused on their customers. The idea is to have a unified enterprise that can respond to those signals. That is an efficient way of reducing total logistics costs.









X Cancel